La découverte des procédés de production massive de l’acier par la filière haut-fourneau a largement contribué à l’essor de la société moderne. L’acier est devenu indispensable pour la production d’infrastructures et de biens divers tels que les chemins de fer, les ponts, les avions, les voitures, les vélos, les machines à laver ou encore les réfrigérateurs.
En savoir plus sur le projet
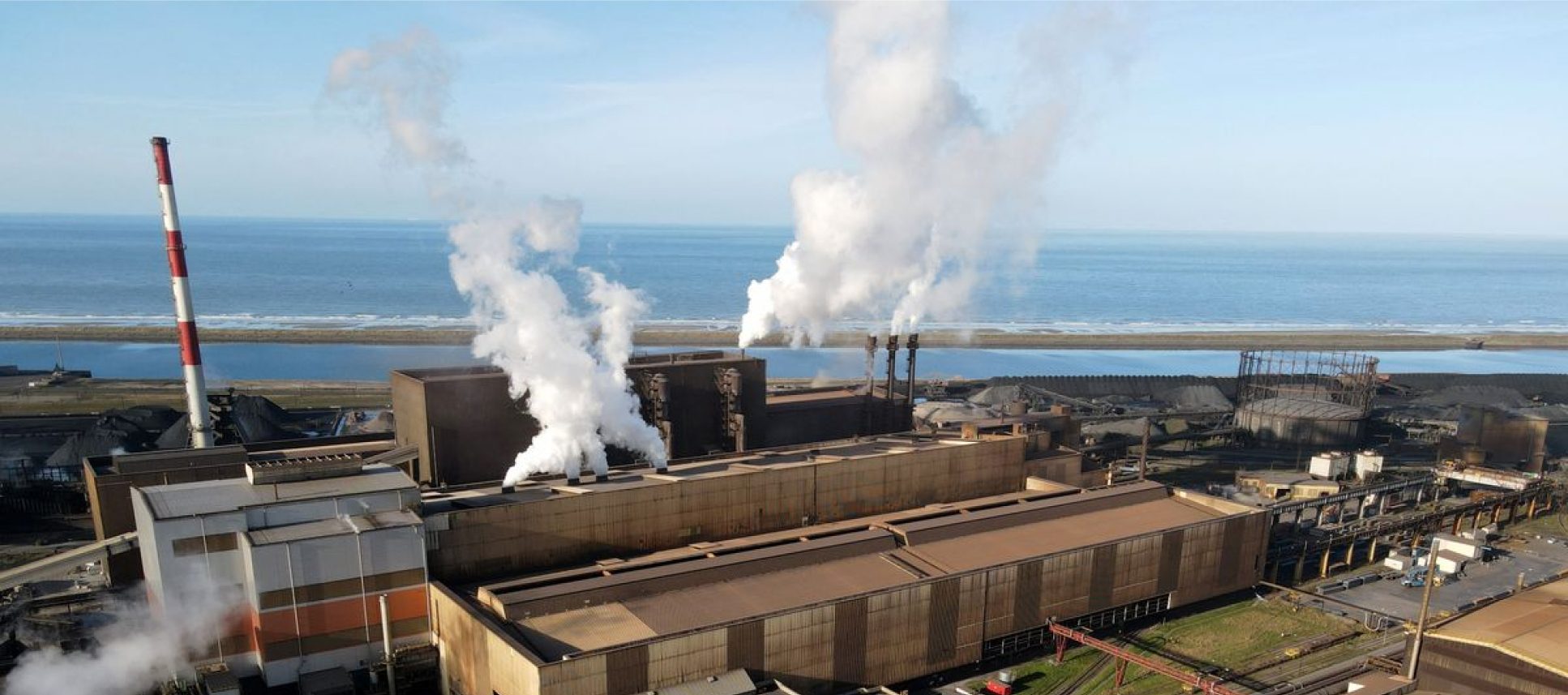
La décarbonation de l’industrie
Le réchauffement climatique est l’une des problématiques mondiales majeures. L’augmentation de l’effet de serre est la cause principale du réchauffement climatique observé ces dernières décennies. Elle est induite par les émissions de gaz à effet de serre (dont le CO2) provoquées par l’activité humaine, et en particulier par la production d’énergie issue de combustibles fossiles. Aussi, en France comme dans le reste de l’Europe, les politiques énergétiques favorisent-elles dorénavant les technologies sobres en carbone.
En conséquence, les politiques énergétiques en France et en Europe favorisent désormais les technologies neutres en carbone.
15
millions de tonnes par an
26k
emplois directs
3ème
rangs des États producteurs
Dunkerque : le premier hub français de décarbonation industrielle
L’Accord de Paris de 2015 a établi un cadre international pour lutter contre le réchauffement climatique. En réponse, l’Union européenne a fixé des objectifs ambitieux pour ses États membres. En France, la Stratégie Nationale Bas Carbone (SNBC), encadrée par des lois de 2015 et 2019, vise à réduire de moitié les émissions industrielles d’ici 2050.
Le bassin industriel de Dunkerque, responsable de 21 % des émissions des industries manufacturières françaises, a lancé plusieurs initiatives locales pour réduire ses émissions. Ces initiatives comprennent le collectif « CO₂ et industries » en 2018 et le manifeste « CO₂, Industries et Territoires » en 2019. Actuellement, plus de 3 milliards d’euros d’investissements sont prévus d’ici 2030 pour soutenir ces actions.
Le programme de la décarbonation
Le programme de décarbonation d’ArcelorMittal France
L’objectif de la décarbonation est de diminuer l’empreinte carbone pour lutter contre le changement climatique. La décarbonation d’ArcelorMittal Dunkerque, plus grand site sidérurgique français, va jouer un rôle crucial. En effet, le procédé de fabrication actuel consomme une grande quantité de charbon, occasionnant des émissions de 1,8 tonne de CO₂ par tonne d’acier produite.
Augmenter l’utilisation de l’acier recyclé
Le premier levier vise à augmenter l’utilisation d’acier recyclé, en remplacement de la fonte, qui est particulièrement émettrice de CO₂. Grâce aux travaux initiés en 2022, le taux d’acier recyclé a doublé sur le site de Dunkerque. Ce levier a déjà permis de diminuer de 8 % les émissions de CO₂ du site de Dunkerque.
Produire de l’acier à basse émission de CO2
Le projet de production d’acier à basse émission de CO2, qui correspond au deuxième levier et que propose ArcelorMittal pour le site de Dunkerque dans le cadre de cette concertation, consiste à changer profondément le procédé de fabrication de l’acier sur le site, c’est-à-dire à abandonner le recours au charbon et au coke, et à réduire le minerai de fer directement avec du gaz naturel dans un premier temps, puis avec un mix de gaz naturel et d’hydrogène décarboné, la part de ce dernier étant augmentée progressivement.
«Smart carbon» : captage, réutilisation et stockage du CO2
Le troisième levier consiste à capter le CO₂ résiduel. Une fois purifié, ce CO₂ peut être transporté vers différentes destinations. Il peut être utilisé dans différentes industries. Une alternative est le stockage dans des couches géologiques profondes, particulièrement celles sous-marines qui contenaient initialement du gaz naturel.
La mise en oeuvre
La mise en œuvre du nouveau procédé est prévue avec les installations suivantes :
Une unité de réduction directe du fer : l’unité de réduction directe tire son nom du procédé, qui consiste à réduire, par du gaz naturel dans un premier temps, les oxydes de fer (naturellement présents dans le minerai de fer) en fer métallique pré-réduit sans le faire fondre. L’innovation principale de la filière consiste à séparer l’opération de réduction de celle de fusion, dont l’association simultanée au sein des hauts-fourneaux nécessitait jusqu’alors l’utilisation de carbone sous forme de coke.
Deux fours électriques (à arc électrique) : les deux nouveaux fours prévus sont à arc électrique, fonctionnant avec du courant alternatif (le charbon, en tant que source d’énergie de la production d’acier, sera remplacé par l’électricité). Ils utilisent l’énergie dégagée par les arcs électriques qui se forment entre leurs 3 électrodes en graphite. L’objectif de cette étape est triple : terminer la réduction du fer initialement pré-réduit, fondre l’acier recyclé et le fer réduit et éliminer les impuretés indésirables.
Deux fours électriques poches qui permettent l’affinage de l’acier liquide et l’ajustement de sa température avant les étapes ultérieures de fabrication jusqu’à la coulée des brames d’acier.
→ Les produits sortis des fours seront ensuite conduits dans des installations existantes (métallurgie secondaire, coulées continues) afin de produire l’acier final. Ainsi, le renoncement aux hauts-fourneaux permet de décarboner partiellement le procédé en utilisant du gaz naturel pour la réduction et de l’énergie électrique pour la fusion. L’autre innovation de cette technologie consiste à pouvoir recourir également à d’autres gaz comme l’hydrogène afin de décarboner davantage le procédé.
→ Dans le but d’assurer la construction et la mise en service des nouveaux outils de production et la continuité des activités actuelles, une étape essentielle sera la préparation du site et la libération des espaces nécessaires. Parmi les activités préparatoires, sont prévues la relocalisation des stocks de charbon (et de boulettes de minerai de fer) et la réorganisation d’activités propres à ArcelorMittal ou à des prestataires déjà présents sur le site de Dunkerque.
→ Par la suite, le montage des nouveaux équipements privilégiera une livraison par la mer des plus volumineux déjà en grande partie assemblés. En contrepartie, des moyens de manutention lourds seront nécessaires sur site (grues de fortes capacités) pour envisager le levage de ces modules.
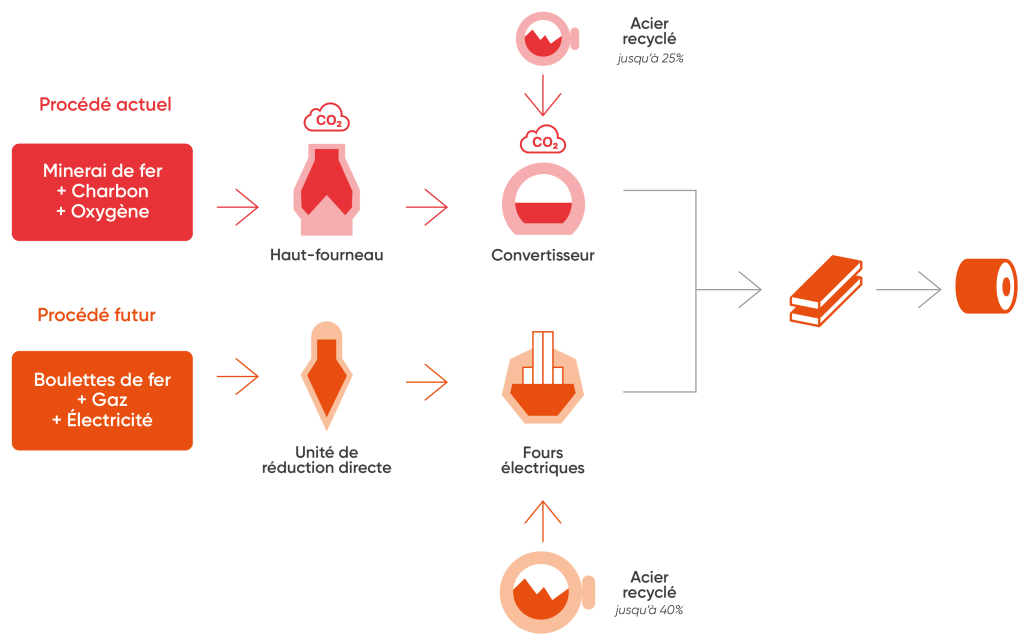
On vous explique
→ Haut-fourneau : Installation utilisée pour produire de la fonte à partir de minerai de fer et de charbon.
→ Unité de réduction directe : Installation utilisant des gaz pour réduire le fer sans passer par le processus de fusion traditionnel du haut fourneau.
→ Convertisseur : Récipient métallique utilisé pour transformer la fonte liquide en acier en injectant de l’oxygène.
→ Fours électriques : Équipement utilisé pour fondre le fer pré-réduit et l’acier recyclé en utilisant de puissants arcs électriques.